Table of Contents
Fused Deposition Modeling (FDM), alternatively referred to as Fused Filament Fabrication (FFF), stands as a cornerstone of additive manufacturing and 3D printing technology. Revered for its accessibility and far-reaching utility, FDM has become an indispensable tool for hobbyists, seasoned professionals, and industrial stakeholders. This comprehensive analysis explores the intricacies of FDM, providing insights into its functional mechanisms, diverse applications, strategic advantages, inherent challenges, and its growing role in driving innovation across sectors.
Also Read: 3D Printing Technologies Overview: Benefits, Applications, and Future Impact
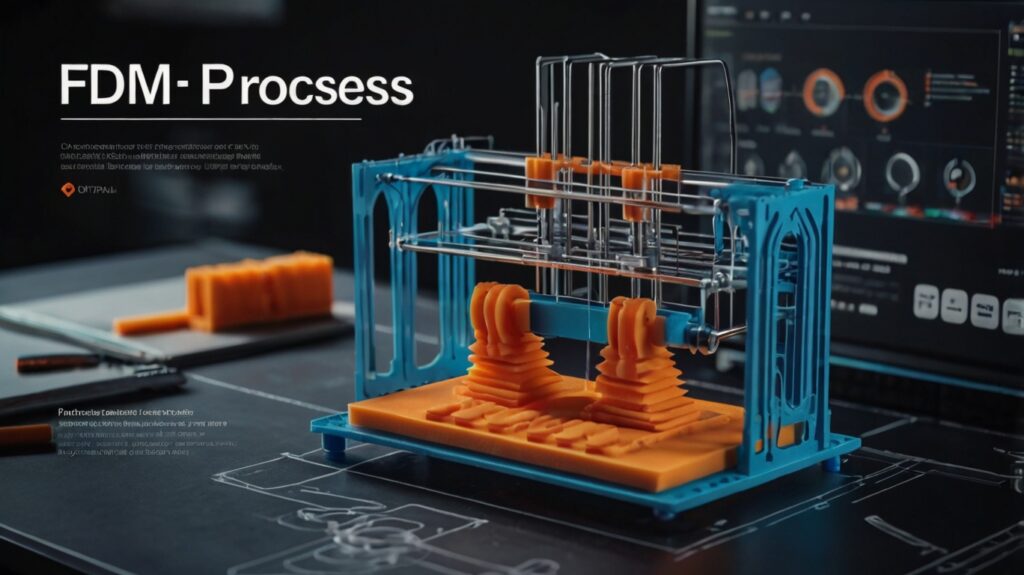
What is Fused Deposition Modeling (FDM)?
FDM is an additive manufacturing process predicated on the sequential layering of thermoplastic filaments to produce three-dimensional structures. Enabled by digital blueprints created via Computer-Aided Design (CAD) software, the technology melds precision with accessibility. From rudimentary prototypes to complex industrial components, FDM continues to demonstrate unmatched versatility across myriad applications.
The FDM Workflow
The FDM fabrication process consists of four cardinal stages:
- Model Design
- This phase begins with the conceptualization and digital modeling of the object using CAD software. Advanced design methods, such as parametric modeling, bolster flexibility and precision, empowering engineers to iterate designs rapidly.
- Slicing software translates the completed model into G-code, delineating a stepwise roadmap for material deposition during printing.
- Slicing
- During this intermediary phase, the CAD design is fragmented into fine horizontal layers. High-caliber slicing software optimizes parameters, including infill percentages, print speed, and necessary support structures, to ensure accuracy and efficiency.
- Printing
- Thermoplastic filaments are extruded via heated nozzles, deposited layer by meticulous layer upon the build platform. Advanced printers equipped with dual-nozzle capabilities afford multi-material configurations, supporting complex designs that marry form and function.
- Post-Processing
- Final refinements include removing support structures, sanding surfaces, and applying chemical treatments to smooth finishes. These post-processing techniques enhance both the visual and mechanical attributes of printed components, paving the way for specialized use cases.
Materials Utilized in FDM
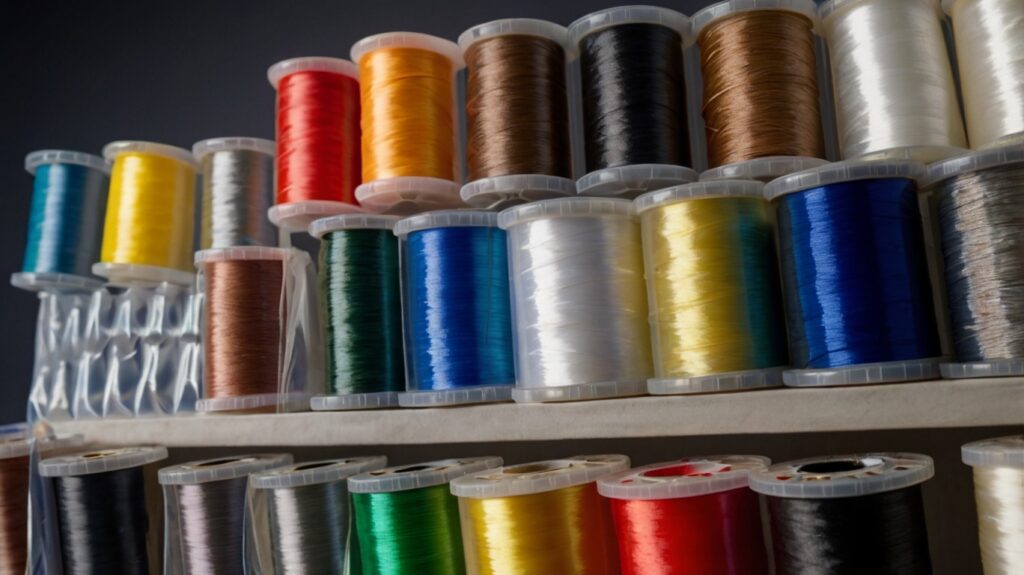
FDM accommodates a robust array of thermoplastic materials tailored for different operational demands. Each material’s properties govern its utility, spanning simple household applications to industrial engineering challenges.
Material | Characteristics |
---|---|
PLA (Polylactic Acid) | Biodegradable, eco-friendly, suitable for aesthetic-focused projects |
ABS (Acrylonitrile Butadiene Styrene) | Heat-resistant, durable, optimal for engineering and structural components |
PETG (Polyethylene Terephthalate Glycol) | Combines chemical resilience with ductility, versatile for functional use |
Nylon | Notably robust and flexible, suited for parts experiencing dynamic loads |
Composite Filaments | Enhanced with fibers like carbon, optimizing weight-strength balance |
Material Recommendations
- PLA: Ideal for lightweight prototypes and environmentally conscious applications.
- ABS/Nylon: Applicable to heavy-duty and heat-resistant products.
- Composite blends: Useful in performance-critical or aesthetic-intensive environments.
Advantages of FDM
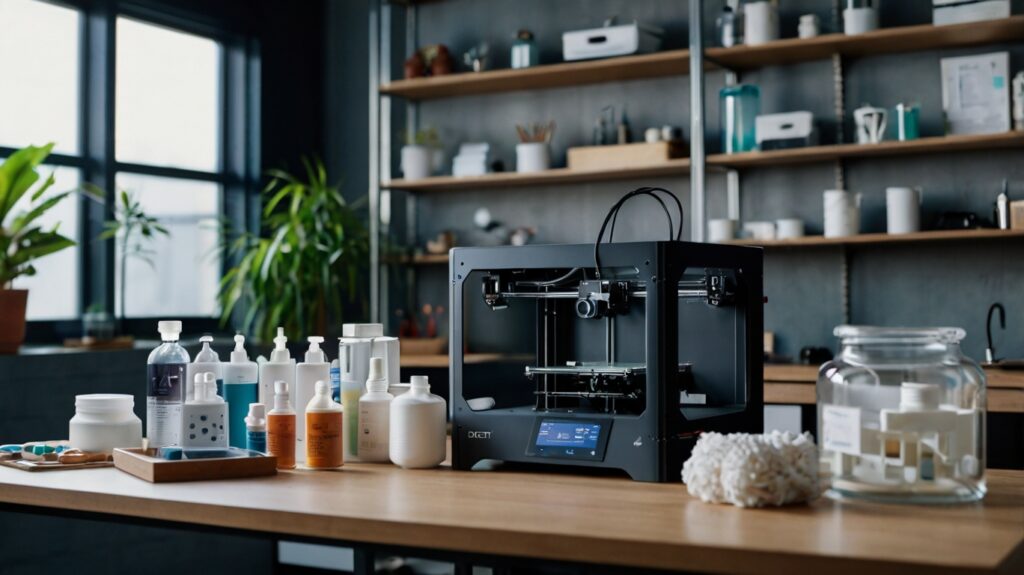
- Relative affordability is a hallmark of FDM, with accessible hardware and low-cost consumables. By bypassing conventional production molds, businesses reduce prototyping expenses dramatically, especially in small-batch production scenarios.
- User-friendly interfaces, streamlined workflows, and extensive online resources render FDM an approachable technology, even for those lacking prior expertise. This democratization expands its appeal across demographic strata.
- Supporting an extensive spectrum of thermoplastics, FDM affords users versatility to align material selection with specific mechanical, thermal, or aesthetic requirements.
- With rapid fabrication cycles, FDM empowers iterative development, enabling designers and engineers to validate, refine, and evolve their projects expeditiously.
- FDM’s adaptability permits bespoke applications, including medical devices, automotive parts, and one-of-a-kind art installations.
Challenges Associated with FDM
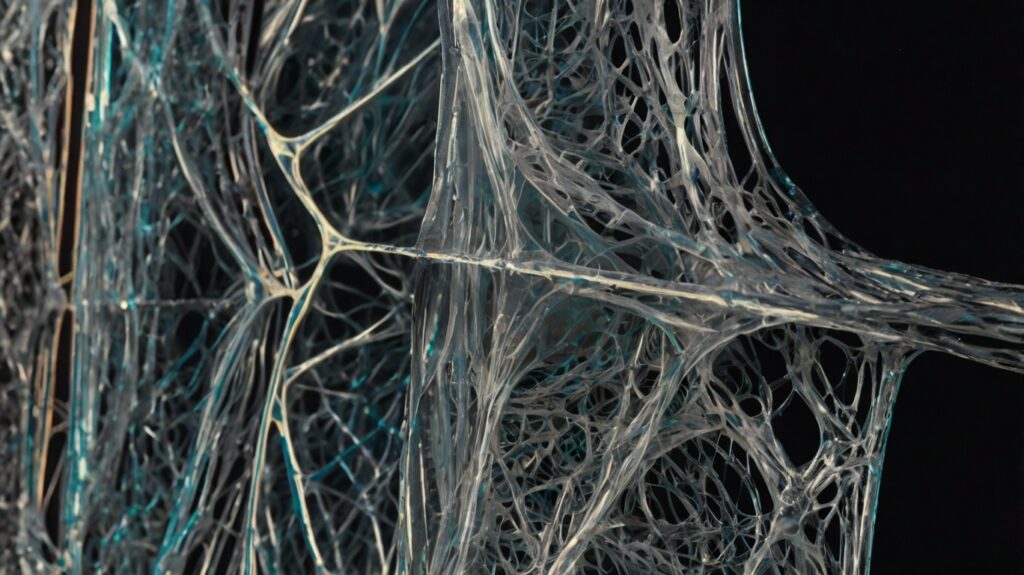
While transformative, FDM is not devoid of limitations. Understanding and mitigating these challenges is essential for realizing its full potential.
Inter-layer Bonding
- Weak inter-layer adhesion can undermine structural integrity. Engineering strategies such as adjusting nozzle temperature and optimizing print settings alleviate these vulnerabilities.
Surface Texture and Finish
- Characteristic layer striations necessitate additional post-processing, like sanding or vapor polishing, to achieve high aesthetic or aerodynamic standards.
Precision Constraints
- In micro-fabrication, FDM’s resolution may fall short when contrasted with technologies like SLA or DLP printing. Innovations in nozzle design continue to expand its fine-detail capabilities.
Material Limitations
- Many standard FDM materials lack high resistance to environmental stressors. However, ongoing advances in filament science, such as the introduction of engineering-grade resins, are addressing these deficits.
Applications of FDM
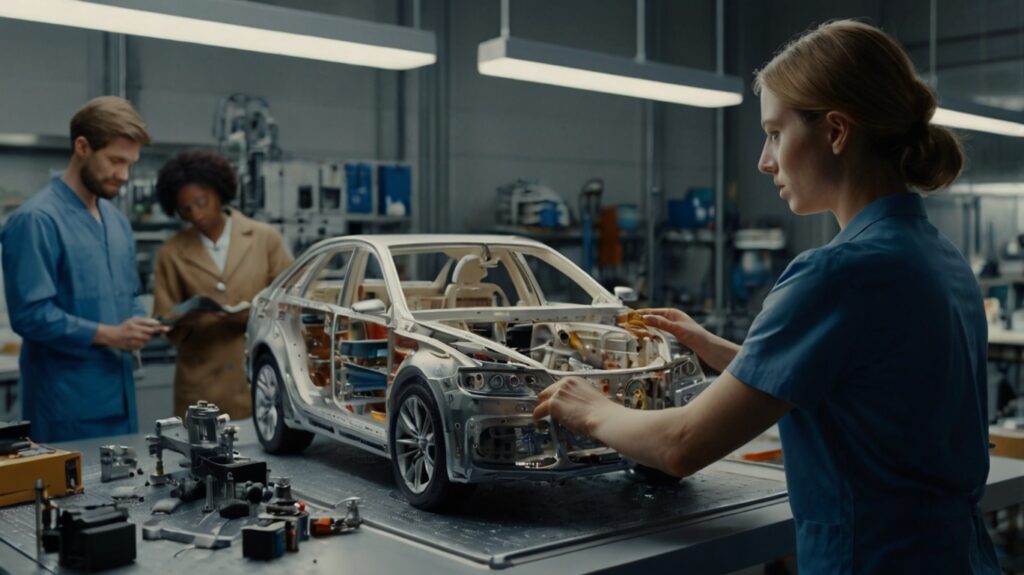
Prototyping and Product Development: From the automotive sector to academia, FDM underpins the creation of conceptual and functional prototypes, expediting design validation processes.
Biomedical Engineering: FDM fabricates cost-effective anatomical models and custom prosthetic devices, enriching medical training and elevating patient care through personalization.
Aerospace Engineering: The lightweight yet mechanically resilient properties of FDM-manufactured components make them indispensable in aerospace engineering, enhancing both efficiency and sustainability.
Niche Consumer Goods: Through bespoke printing, FDM caters to entrepreneurial endeavors, enabling small-scale production of artistic, functional, or highly customized consumer products.
FAQs
How does FDM differ from SLA?
FDM emphasizes cost and scalability, while SLA excels in precision and surface smoothness. Choice hinges on application-specific needs.
Is FDM suitable for producing end-use parts?
With advancements in composite materials and post-processing techniques, FDM is increasingly viable for final-use applications.
What industries benefit most from FDM?
Aerospace, healthcare, education, and consumer goods sectors leverage FDM for its cost, adaptability, and efficiency.
Final Insights
Fused Deposition Modeling (FDM) persists as an adaptive and influential force in the sphere of modern manufacturing. Its seamless integration of affordability, technological adaptability, and material ingenuity positions FDM as both a driver of creativity and an enabler of industrial breakthroughs. For practitioners and innovators alike, FDM remains a linchpin in the pursuit of transformative design and production paradigms.
[…] Also Read : “Fused Deposition Modeling (FDM): Comprehensive Guide to 3D Printing Technology” […]
[…] Fused Deposition Modeling (FDM) […]