Architectural model making is a vital process for architects, designers, and builders. It allows for a tangible representation of a concept, providing a clear, physical depiction of what a structure will look like once completed. This guide aims to provide a comprehensive understanding of architectural model making, offering insights into why it is crucial, the various types of models, a step-by-step guide, materials and techniques used, and tips for both beginners and professionals.
Table of Contents
Introduction
Architectural model making has been an integral part of the design process for centuries. It serves as a bridge between conceptual ideas and their tangible realization, providing both the designer and their clients with a physical representation of a structure. By transforming abstract plans into a 3D form, architectural models help visualize, communicate, and refine designs.
Why Architectural Model Making is Essential
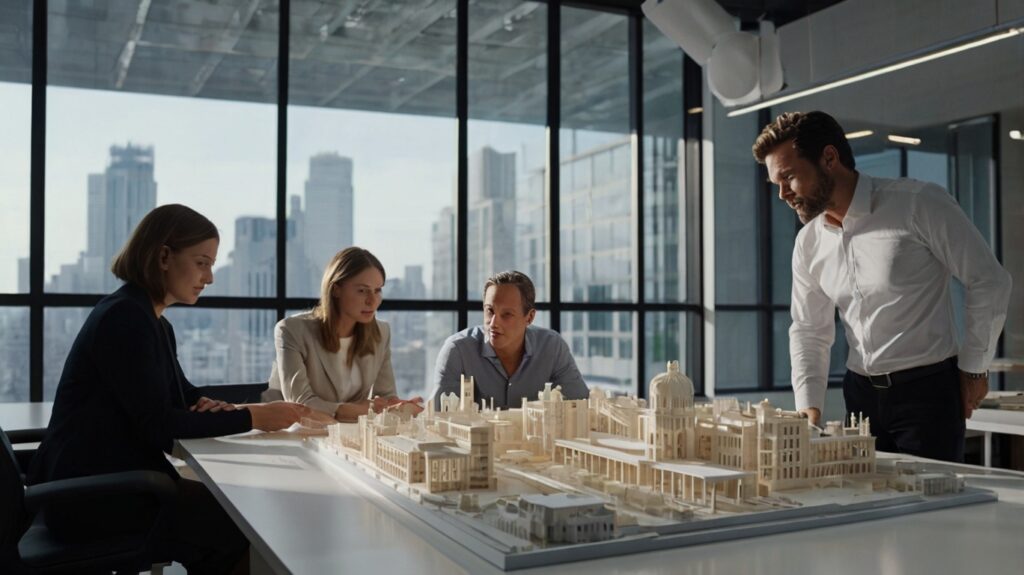
Benefits in Visualizing Designs:
One of the key reasons architects and designers rely on model making is that it allows them to explore their design ideas in a three-dimensional context. It makes it easier to understand the scale, proportions, and spatial relationships between elements of a design. With a model, designers can see how the building will interact with its environment and make informed decisions before construction begins.
Communication Tool for Clients and Stakeholders:
Architectural models are also critical in conveying design ideas to clients, investors, and other stakeholders. A physical model provides a concrete representation of an idea, allowing for better discussions and decision-making. It can also help in securing project approval by providing a clear, understandable visual reference that digital drawings or CAD models might not convey.
Types of Architectural Models
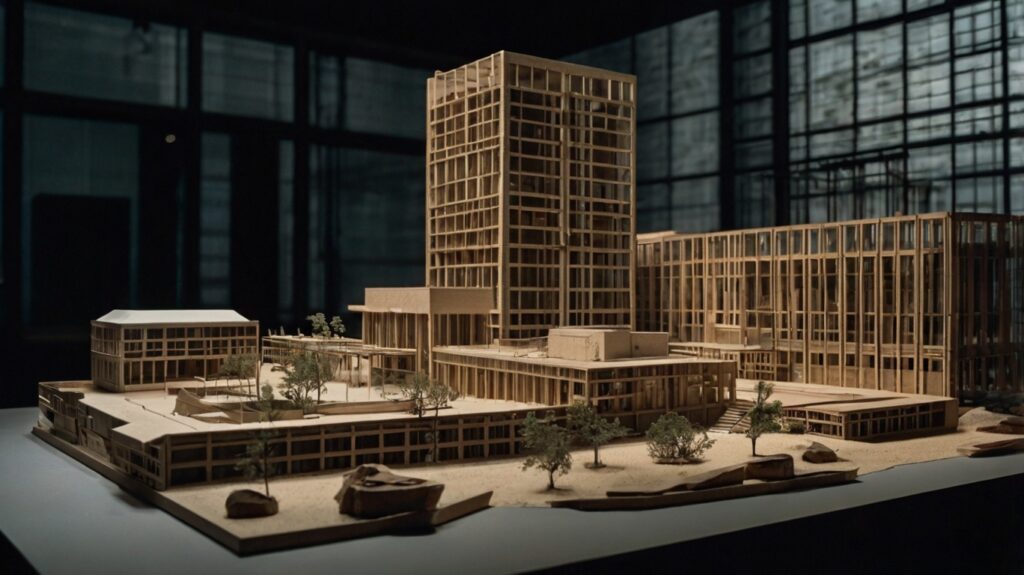
Conceptual Models:
These models are created in the early stages of design to explore the basic form and ideas behind a project. They are usually simple and often abstract, focusing on massing, shape, and overall volume rather than detailed accuracy.
Working Models:
Working models are more detailed than conceptual ones and are typically used to test the functionality of a design. They might include movable parts or internal components to simulate how the building will function in real life.
Presentation Models:
Used for client presentations or public exhibitions, presentation models are highly detailed and refined to showcase a design’s aesthetics. These models aim to impress, highlighting the beauty and final appearance of the building.
Scale Models:
These models represent the full design but are built to a smaller, proportional scale. They help architects and clients better understand the overall scale and proportions of the design, and can be a mix of conceptual or presentation models.
Step-by-Step Guide: How to Make Architectural Models
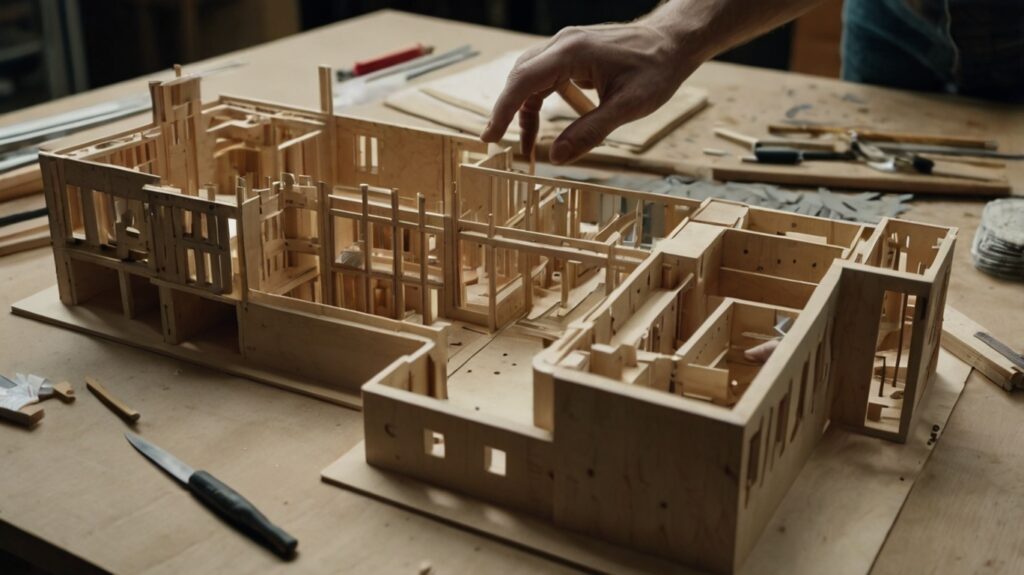
Planning and Selecting the Type of Model:
Before beginning the construction of a model, it’s important to decide which type of model is most appropriate based on the project’s goals and stage of development. Conceptual models can be simple and quick, while presentation models require more attention to detail and time.
Choosing Materials Based on the Model’s Purpose:
Different materials are suited for different types of models. Foam board, for example, is light and easy to cut, making it ideal for quick conceptual models. Balsa wood or MDF is used for more detailed models, while plastics and acrylic are perfect for presentation models that require a more refined finish.
Essential Tools and Setup:
A well-organized workspace is crucial for efficient model making. You’ll need basic tools like utility knives, rulers, compasses, tweezers, and scissors for cutting and shaping materials. More advanced tools may include laser cutters or 3D printers for precision work.
Building the Model (Basic Process):
- Start by preparing your base and framework.
- Cut the materials to the required shapes and sizes using appropriate tools.
- Assemble the parts, ensuring the model’s scale is consistent.
- Apply finishes such as paint or textures if necessary, especially for presentation models.
Materials and Techniques in Architectural Model Making
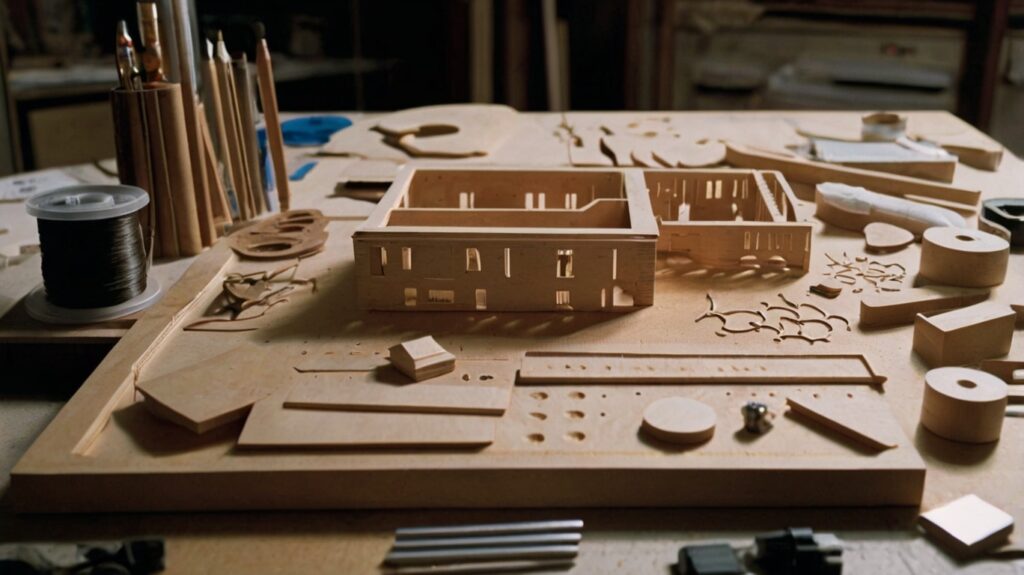
Overview of Materials:
- Foam Board: Light, easy to cut, and widely used for basic models.
- Balsa Wood: Soft, lightweight wood ideal for precision work in more detailed models.
- MDF (Medium Density Fiberboard): A durable material used for structural models or working models.
- Acrylic: Transparent material often used for presentation models, allowing for clean lines and polished finishes.
- Cardboard: Cheap and versatile, suitable for prototyping or less complex models.
- Plastics: Used in detailed, modern models, often with advanced techniques like 3D printing.
Cutting and Assembly Techniques:
- Hand Tools: For most model-making projects, traditional cutting tools such as utility knives and scissors are sufficient. Precision is key.
- Laser Cutting: This technology allows for precision cutting of materials, which is particularly useful for intricate details and complex geometries.
- 3D Printing: Perfect for creating highly detailed and intricate components that would be difficult or impossible to achieve with traditional hand tools.
Common Materials Used in Architectural Model Making
Material | Best Used For | Characteristics |
---|---|---|
Foam Board | Conceptual models, quick prototypes | Light, easy to cut, inexpensive |
Balsa Wood | Detailed and refined models | Lightweight, easy to shape, perfect for fine details |
MDF | Structural or working models | Durable, smooth, but requires power tools for cutting |
Acrylic | Presentation models | Transparent, polished, requires precision cutting |
Cardboard | Prototyping, simple models | Inexpensive, easy to work with, but not very durable |
Plastics | Detailed, modern models | Versatile, durable, but requires advanced tools like 3D printing |
Architectural model making requires a variety of materials, each chosen based on the specific needs of the model being created. The materials not only affect the model’s appearance but also its durability, ease of construction, and the overall look and feel of the finished product. Here’s a breakdown of some of the most common materials used in architectural model making:
Foam Board
- Best Used For: Conceptual models, quick prototypes, and early-stage design exploration.
- Characteristics:
Foam board is one of the most widely used materials in architectural model making due to its light weight and ease of manipulation. It typically consists of a layer of foam sandwiched between two thin layers of paper or plastic. It’s easy to cut, making it ideal for quickly creating basic shapes, massing models, or simple mock-ups. Foam board is especially useful for creating quick, low-cost prototypes or for representing large volumes in a conceptual model. - Advantages: Lightweight, inexpensive, easy to cut, and readily available.
- Limitations: Not as durable as other materials and may not be suitable for highly detailed or long-term models.
Balsa Wood
- Best Used For: Detailed and refined models, especially for presentation models or when fine details are needed.
- Characteristics:
Balsa wood is a lightweight, softwood material that is easy to cut, sand, and shape. It’s often used for models that require precision, such as architectural presentation models. Balsa is available in various thicknesses, making it versatile for different aspects of a model, from framing to intricate detailing. It’s particularly valued for its workability, allowing the designer to achieve a smooth finish with relatively little effort. - Advantages: Easy to shape and carve, lightweight, perfect for detailed work.
- Limitations: Can be fragile and may break or splinter, especially in thin sections.
MDF (Medium Density Fiberboard)
- Best Used For: Structural or working models where durability and sturdiness are required.
- Characteristics:
MDF is a type of engineered wood made from compressed wood fibers. It is denser and more durable than balsa wood, making it a good choice for building more substantial, long-lasting models. It can be used for the base or core of a model, as well as for creating detailed, hardwearing components. MDF requires more advanced tools to cut, such as saws or laser cutters, but it offers a smoother finish and can handle detailed carving and texturing. - Advantages: Durable, smooth surface, suitable for larger models or structural parts.
- Limitations: Heavier than other materials, and can be difficult to work with without the right tools.
Acrylic
- Best Used For: Presentation models, transparent or refined details, and visual effects.
- Characteristics:
Acrylic, also known as Perspex, is a clear, hard plastic that’s commonly used for creating sleek, polished architectural models. It can be cut and shaped using laser cutters, allowing for precise, clean lines. Acrylic is used for both aesthetic and functional purposes, often as a material for windows, glazing, or for adding a polished finish to presentation models. Its transparency makes it an excellent choice for highlighting specific aspects of a design, such as interior spaces or light features. - Advantages: Transparent, smooth, and modern-looking; perfect for sleek, polished finishes.
- Limitations: Requires specialized tools for cutting and shaping, can be brittle.
Cardboard
- Best Used For: Prototyping, simple models, or quick massing models.
- Characteristics:
Cardboard is one of the most inexpensive and easily accessible materials for model making. It comes in many forms, from corrugated board for larger models to thin, flexible cardboard sheets for finer work. While cardboard isn’t as durable as other materials, it’s ideal for quick prototypes or when you need to rapidly explore different design options without a significant investment in materials. It can be easily cut, folded, and glued together. - Advantages: Inexpensive, easy to use, and readily available.
- Limitations: Less durable, may warp or degrade over time, and doesn’t provide the level of refinement needed for presentation models.
Plastics
- Best Used For: Detailed, modern models, especially when precision and intricate parts are needed.
- Characteristics:
Plastics used in architectural model making are often chosen for their versatility, durability, and precision. These materials include various types of sheets, such as styrene or PETG, which can be cut, drilled, and shaped for detailed components. Plastics are frequently used for intricate parts such as windows, railings, or small-scale details that need to be durable and precise. 3D printing also uses plastic filaments, such as PLA or ABS, to create highly detailed components that might otherwise be difficult to achieve manually. - Advantages: Versatile, durable, and allows for high precision, especially with modern digital fabrication methods like 3D printing.
- Limitations: Can be more expensive than other materials and may require specialized tools to work with.
Tips for Beginners and Professionals
Best Practices for Efficient Model Making:
- Start with Simple Models: For beginners, it’s important to start with basic models to master the fundamentals of cutting, assembling, and finishing before tackling more complex projects.
- Use a Clean Workspace: Keeping your workspace organized and clean will reduce the risk of mistakes and help maintain the quality of your work.
- Consider Scale: Pay attention to the scale of your model. A mismatch between the scale of the model and the real-world structure can lead to unrealistic results.
- Use the Right Tools: Don’t rely on makeshift tools. Invest in proper cutting and assembly tools to achieve professional-quality results.
Avoiding Common Mistakes:
- Underestimating the Time Required: Model making takes time and attention to detail. Be realistic about how long it will take to complete your model.
- Skipping the Planning Stage: Skipping detailed planning and moving straight into the construction phase often leads to mistakes that are hard to fix later on.
- Overcomplicating the Design: Especially for beginners, trying to make overly detailed models too soon can be frustrating. Start simple, then progress to more complex designs.
Conclusion
Architectural model making is an essential tool in the design process that allows architects to bring their ideas to life. Whether it’s for visualization, communication, or design exploration, models provide valuable insights and feedback. By experimenting with various materials and techniques, both beginners and experienced professionals can enhance their model-making skills and continue to refine their craft. As technology advances, tools like laser cutting and 3D printing offer new opportunities, but the foundational skills of planning, material selection, and precision remain at the core of the craft.
Remember, model making is as much about creativity and exploration as it is about precision and skill. Keep experimenting and refining your approach, and you’ll be able to create models that not only showcase your ideas but also elevate them.
Also Read : “Mastering 3D Printing: Selecting the Best Filament for Your Needs”