Table of Contents
3D printing has redefined the paradigms of manufacturing, prototyping, and creative hobbies by offering unparalleled flexibility and innovation. Central to this transformative process is slicing—an intricate operation that converts digital designs into meticulously detailed, layer-by-layer instructions for a 3D printer.
The role of slicing extends far beyond mere translation of data; it establishes the foundation for precision, material efficiency, and structural integrity in the final printed object. While rudimentary slicing methods can address straightforward projects, the advent of advanced slicing techniques has significantly expanded the horizons of this technology, enabling enhanced quality, reduced waste, and the realization of complex geometries previously deemed unattainable.
This comprehensive guide explores the Advanced Slicing Techniques that are reshaping the capabilities of 3D printing. By delving into these methods, you will uncover how they elevate not only the quality of printed objects but also the efficiency of production workflows. Let us embark on this exploration of cutting-edge slicing innovations and their transformative impact on modern 3D printing.
What is Slicing in 3D Printing?
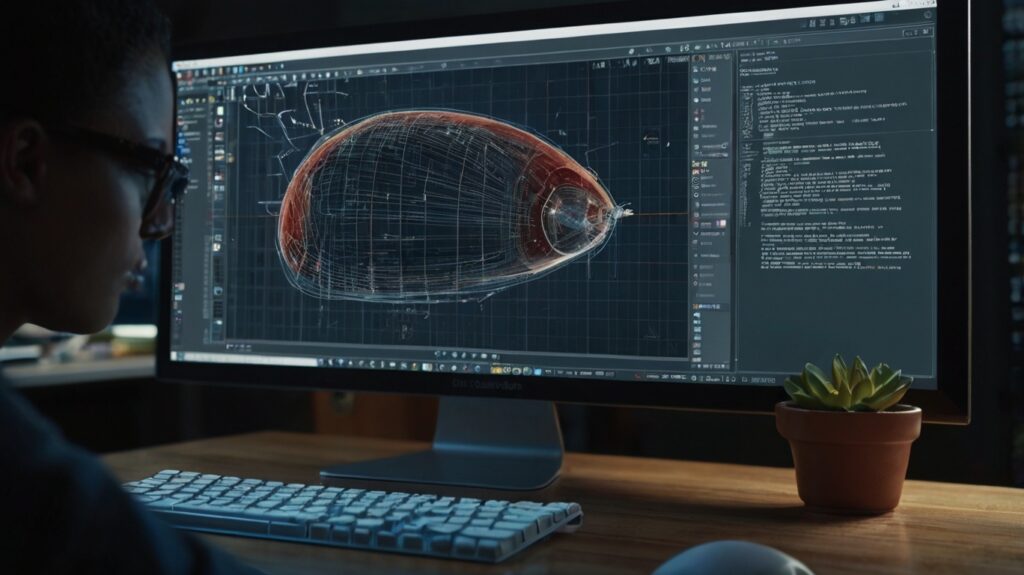
Slicing is the cornerstone of 3D printing, involving the conversion of a digital 3D model into horizontal stratifications and the subsequent generation of G-code. This G-code serves as the operational blueprint for the printer, dictating every nuanced movement, material deposition, and associated parameter. Beyond its functional role, slicing embodies the synthesis of design and production, bridging the conceptual and the tangible with precision and intent.
Standard slicing techniques, while effective for basic models, are inherently constrained when faced with intricate geometries, stringent tolerances, or material optimization needs. Advanced slicing techniques, in contrast, introduce adaptive mechanisms and sophisticated algorithms that address these limitations.
They provide enhanced precision, optimize material use, and enable complex forms to be manufactured with remarkable fidelity. Embracing these cutting-edge methodologies empowers users to fully exploit the potential of their 3D printing systems, delivering superior outcomes and facilitating projects of unprecedented complexity.
Advanced Slicing Techniques
1. Adaptive Slicing: Balancing Detail and Speed
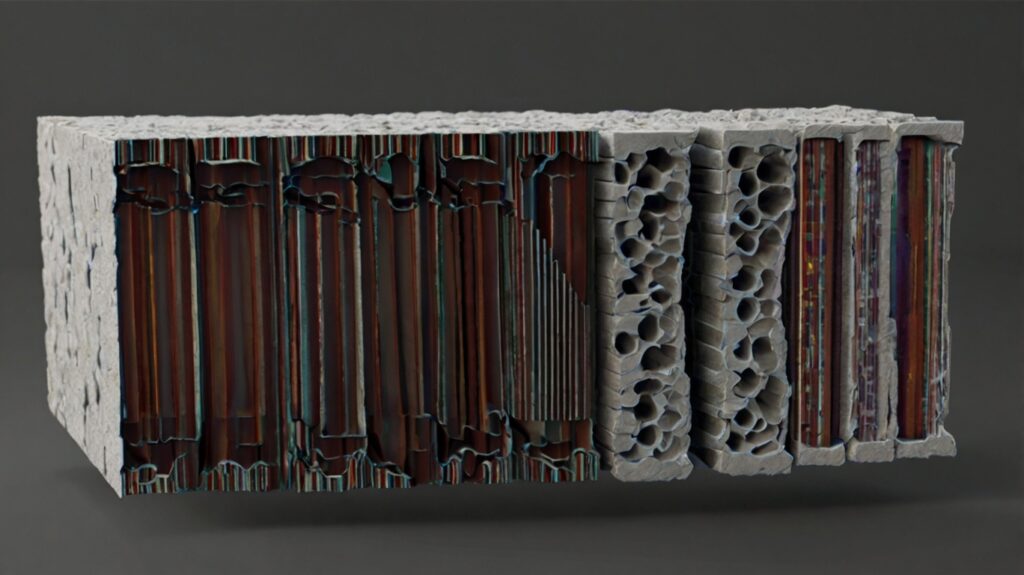
- What it is: Adaptive slicing transcends the limitations of uniform slicing by dynamically adjusting layer thickness in response to the geometry of the model. This process entails an in-depth analysis of the design’s contours, allowing thinner layers to be applied to regions demanding high resolution and thicker layers for less critical areas.
- Benefits:
- Captures fine details and intricate curves with unparalleled accuracy through the strategic use of thinner layers.
- Significantly accelerates the production process by employing thicker layers in simpler sections, optimizing both time and material efficiency.
- Enhances surface smoothness, mitigating the need for extensive post-processing, and yields aesthetically superior prints.
- Reduces overall material consumption, making it an economical option for diverse structural and artistic applications.
- When to use: Adaptive slicing excels in projects requiring a balance of fine detailing and expedited production, such as architectural models, artistic sculptures, and functional prototypes with varying feature complexities.
2. Multi-Axis Slicing: Breaking Free from the Planar Norm
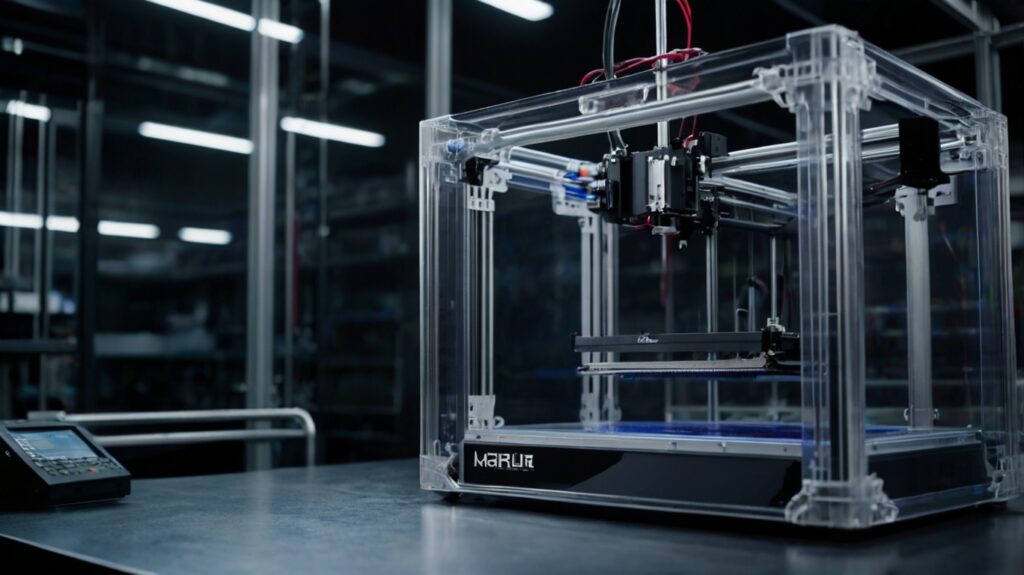
- What it is: Multi-axis slicing introduces a paradigm shift by eschewing conventional planar layering in favor of non-planar slicing paths. Enabled by advanced multi-axis printers, this method integrates rotational and angular movements of the build platform or nozzle to align layers with the model’s natural contours.
- Benefits:
- Eliminates reliance on support structures for overhangs, reducing both material waste and post-production labor.
- Facilitates the creation of stronger components by optimizing layer orientations to better withstand operational stresses.
- Enhances aesthetic appeal by minimizing visible layer lines, producing visually seamless finishes.
- Broadens design possibilities, enabling the fabrication of intricate geometries and organic shapes that are unattainable with planar slicing methods.
- Use case: Particularly valuable for applications involving biomimetic designs, detailed figurines, or engineering components with intricate internal and external features.
3. Direct CAD-Based Slicing
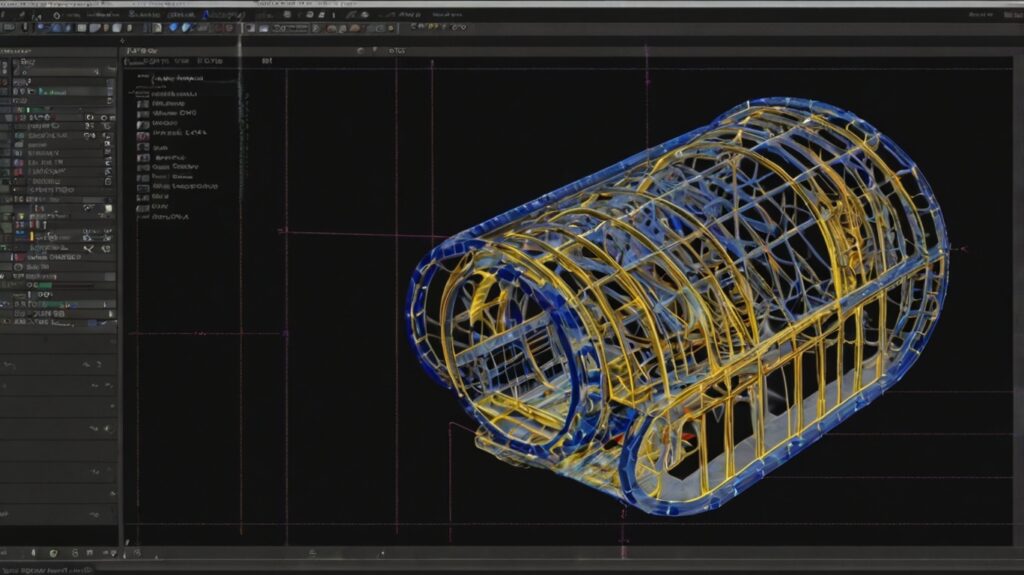
- What it is: Direct CAD-based slicing circumvents the traditional STL conversion process by generating slice data directly from CAD models. This technique leverages the inherent precision of CAD tools to deliver superior accuracy and streamlined workflows.
- Benefits:
- Eliminates common STL-related issues, such as geometry errors or data loss, ensuring the fidelity of the printed model.
- Enhances compatibility with advanced design features, preserving intricate details and ensuring precise replication.
- Simplifies the workflow for CAD-centric users, reducing potential errors associated with file conversions and optimizing productivity.
- Supports seamless integration with advanced printing parameters, further augmenting the quality of the output.
- Best for: This method is indispensable for engineering and industrial applications that demand stringent tolerances, high precision, and integration of complex features.
Key Parameters for Enhanced Slicing
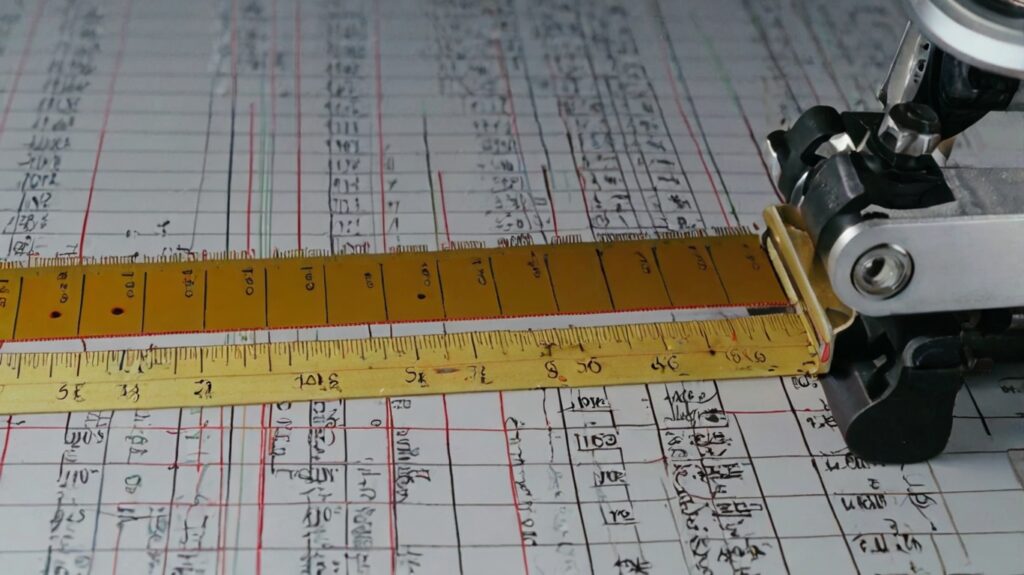
Layer Height
- Smaller layer heights yield superior resolution, capturing minute details but at the cost of extended print durations. Conversely, larger layer heights expedite production but compromise surface quality. The judicious selection of layer height, tailored to the project’s priorities, is crucial for achieving the desired balance between precision and efficiency.
Shell Thickness
- Optimizing shell thickness reinforces structural integrity while enhancing surface quality. Thin shells are ideal for lightweight applications, whereas thicker shells provide robustness for load-bearing components. Adapting shell thickness to specific design needs ensures optimal performance and durability.
Infill Patterns and Density
- The choice of infill patterns, such as honeycomb or gyroid, influences strength, material usage, and weight. Higher infill densities fortify the model but increase print time and resource consumption, necessitating strategic optimization based on functional requirements.
Print Path Optimization
- Sophisticated algorithms optimize nozzle movements, minimizing travel distances and preventing material defects like stringing. This enhances print accuracy and overall efficiency, particularly in complex designs with multiple features.
Error Detection and Preview Tools
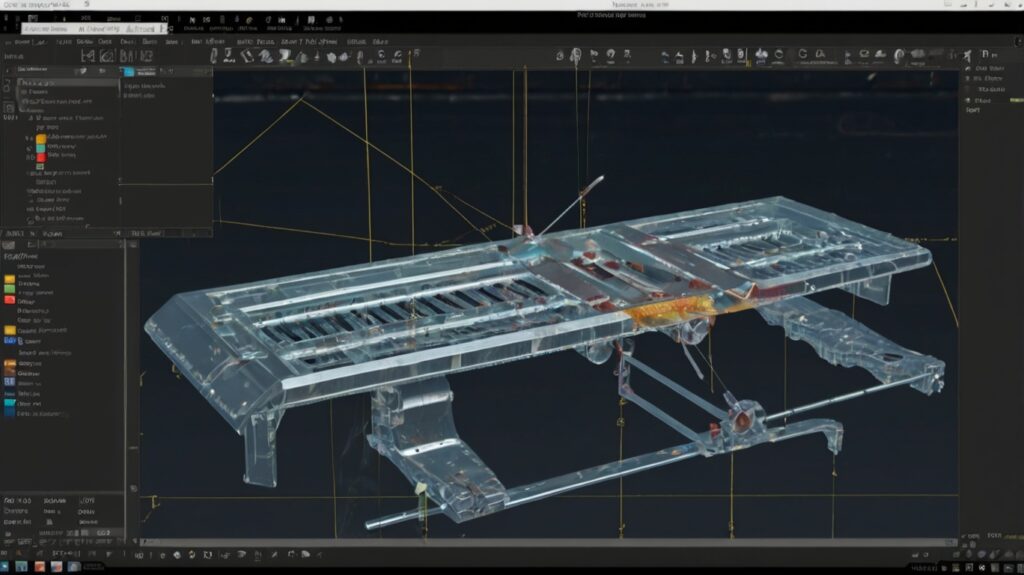
Modern slicing software integrates advanced error-checking mechanisms and visual simulation tools to preemptively address potential issues:
- Error detection: These systems identify structural vulnerabilities, misalignments, and inadequate supports, providing actionable feedback to rectify flaws before printing.
- Previews: Comprehensive simulations offer a detailed visualization of the print process, enabling users to fine-tune settings dynamically, anticipate outcomes, and avert costly mistakes.
Comparison of Slicing Techniques
Technique | Advantages | Best For |
---|---|---|
Uniform Slicing | Simple and fast | Basic models |
Adaptive Slicing | Saves time and material; improves detail | Complex geometries |
Multi-Axis Slicing | Eliminates supports; smoother finishes | Intricate designs |
Direct CAD-Based Slicing | Higher accuracy; avoids STL issues | Precision applications |
Practical Tips for Implementing Advanced Slicing
- Experiment with Layer Heights: Tailor settings to harmonize detail and efficiency.
- Leverage Multi-Axis Features: Unlock new possibilities in design and production with advanced non-planar capabilities.
- Use Cutting-Edge Software: Opt for solutions like PrusaSlicer, Cura, or Simplify3D to exploit sophisticated slicing functions.
- Ensure Printer Calibration: Regular maintenance and accurate calibration are indispensable for realizing the benefits of advanced slicing techniques.
Conclusion
Advanced slicing techniques redefine the potential of 3D printing by addressing limitations of traditional methods and enabling innovative designs. Whether your objective is to achieve intricate detail, optimize production speed, or reduce material usage, these methodologies provide the means to accomplish your goals with precision and ingenuity. By integrating these practices into your workflow, you can harness the transformative capabilities of 3D printing and push the boundaries of creativity and functionality.
FAQs
What is the difference between uniform and adaptive slicing?
Uniform slicing employs consistent layer thickness throughout, while adaptive slicing varies thickness to balance detail and efficiency.
Why should I use direct CAD-based slicing?
Direct CAD-based slicing preserves design integrity, avoids STL-related issues, and ensures high-precision outputs.
Can multi-axis slicing be done on all 3D printers?
No, it requires specialized multi-axis printers capable of non-planar movement.
How do I optimize infill settings?
Select patterns and densities that balance structural strength with material conservation, tailored to your project’s requirements.
What software supports advanced slicing techniques?
Leading software includes Cura, PrusaSlicer, and Simplify3D, each offering unique features to enhance slicing precision and efficiency.