Table of Contents
Introduction
3D printing has revolutionized manufacturing, prototyping, and even art. With various techniques available, choosing the right one for your project can be overwhelming. This guide explores three popular methods: Fused Deposition Modeling (FDM), Stereolithography (SLA), and Selective Laser Sintering (SLS). By understanding their strengths, weaknesses, and ideal applications, you can make an informed decision tailored to your needs.
The Basics of FDM, SLA, and SLS
Each 3D printing technique uses a unique process to create objects, leveraging different technologies and materials to achieve distinct results. Understanding these methods is essential to choosing the right one for your project:
- FDM: Fused Deposition Modeling constructs objects layer by layer using melted thermoplastic filaments. The filament is heated to its melting point and extruded through a nozzle, which moves along pre-defined paths to create each layer. This method is known for its accessibility and affordability, making it popular among hobbyists and small-scale manufacturers.
- SLA: Stereolithography employs a UV laser to cure liquid resin into solid layers. The laser traces the object’s design on the surface of the resin, solidifying it layer by layer. This technique is renowned for its high precision and smooth finishes, making it ideal for applications requiring intricate details and aesthetics, such as jewelry or dental models.
- SLS: Selective Laser Sintering uses a high-powered laser to sinter powdered materials, fusing them into solid structures without the need for support structures. The laser selectively binds the powder layer by layer, resulting in durable and complex geometries. SLS is a go-to choice for industrial applications where strength and functionality are paramount.
By understanding the fundamental processes behind FDM, SLA, and SLS, you can better appreciate their unique advantages and limitations, ultimately helping you select the most suitable technique for your specific needs.
Fused Deposition Modeling (FDM)
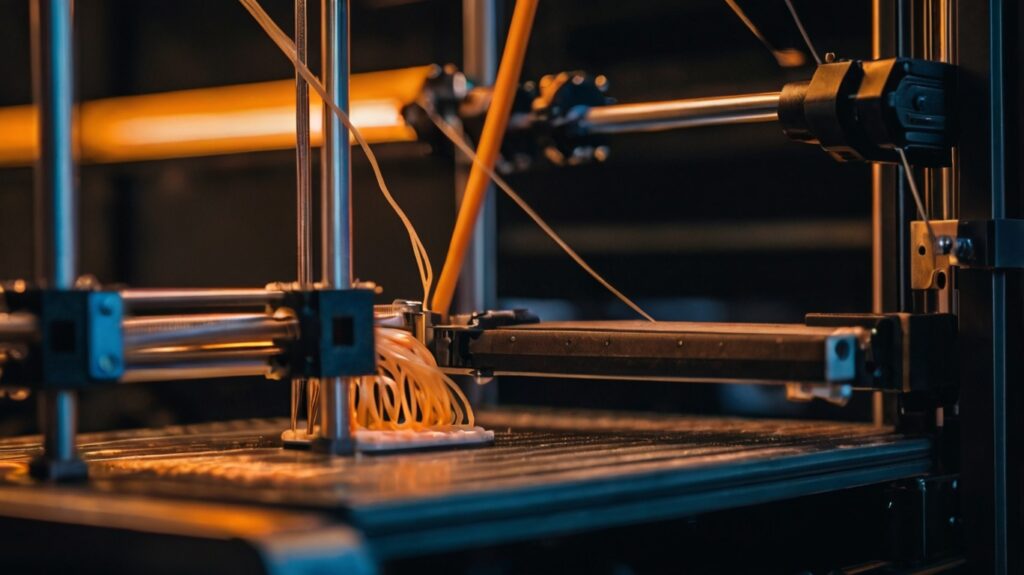
Overview:
- Most accessible and cost-effective technique.
- Commonly used for hobbyist projects, educational purposes, and functional prototypes.
- Frequently adopted by small businesses for rapid prototyping and product testing.
Materials:
- PLA, ABS, PETG, and flexible filaments.
- Specialty filaments, such as carbon-fiber-infused or wood-filled options, are also available for unique applications.
Advantages:
- Low cost and widely available hardware and materials.
- Easy to use with minimal training required.
- Wide range of materials, including biodegradable options like PLA.
- Large build volumes are achievable with certain FDM printers.
Limitations:
- Lower resolution and surface finish compared to SLA and SLS.
- Limited to thermoplastics, which may not meet all industrial requirements.
- Susceptible to warping and layer adhesion issues, especially with ABS.
Stereolithography (SLA)
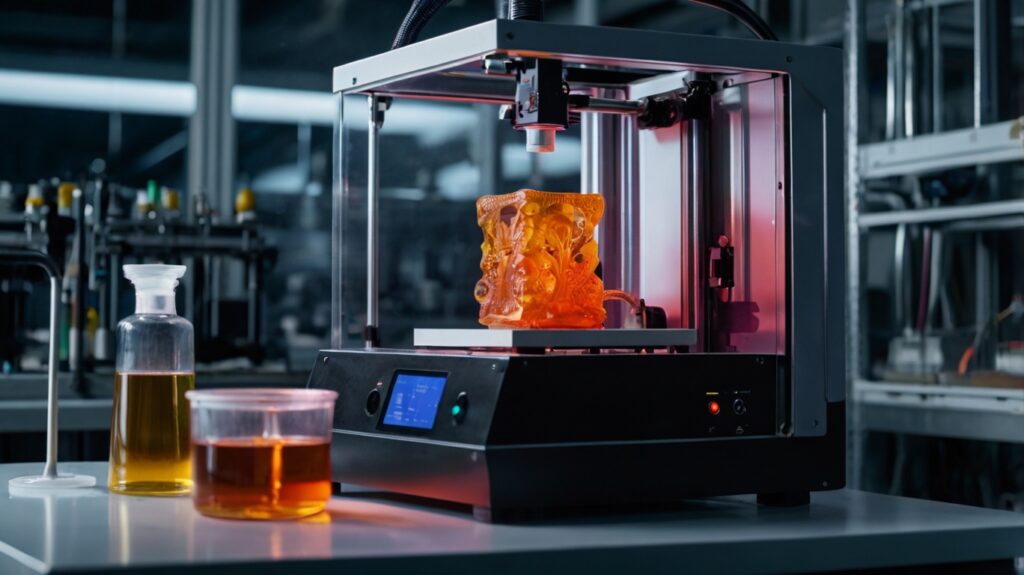
Overview:
- Renowned for its high precision and smooth surface finishes.
- Ideal for detailed prototypes, artistic models, and medical applications such as dental aligners and implants.
- Often used in industries requiring intricate designs and fine detail.
Materials:
- Photopolymer resins.
- Specialty resins for applications like biocompatibility, heat resistance, and flexibility.
Advantages:
- Exceptional detail and accuracy, making it suitable for complex geometries.
- Smooth surfaces reduce the need for extensive post-processing.
- Wide range of resin options tailored to specific industry needs.
Limitations:
- Higher cost for equipment and consumables.
- Requires post-processing, including cleaning and UV curing, which adds to production time.
- Resins can be brittle and less suitable for mechanical applications.
Selective Laser Sintering (SLS)
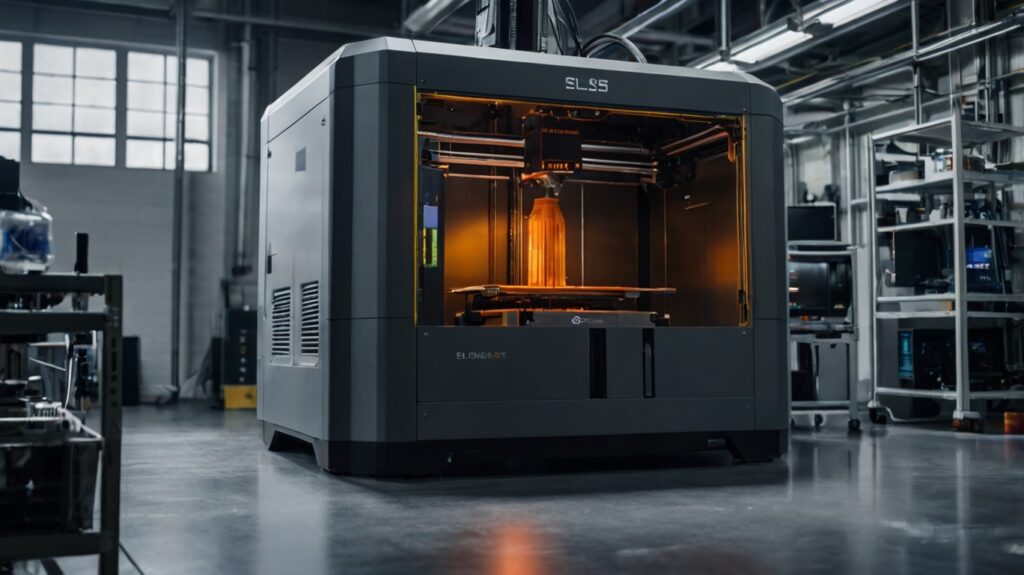
Overview:
- Best suited for industrial applications and complex geometries that demand durability and precision.
- Commonly used for aerospace, automotive, and medical device manufacturing.
- Excellent for producing functional prototypes and low-volume production runs.
Materials:
- Nylon, polyamides, and composites.
- Advanced materials like glass-filled nylon and aluminum powders for enhanced properties.
Advantages:
- No need for support structures, enabling more complex designs.
- Durable and functional parts with excellent mechanical properties.
- High production efficiency with the ability to print multiple parts simultaneously.
Limitations:
- Expensive equipment and materials.
- Requires skilled operators and significant setup time.
- Post-processing, such as powder removal and surface finishing, can be labor-intensive.
Factors to Consider When Choosing a 3D Printing Technique
Budget:
- FDM is the most affordable option for both equipment and materials.
- SLA and SLS involve higher costs due to specialized equipment and materials, with SLS being the most expensive.
Material Requirements:
- FDM: Thermoplastics, with options for specialty filaments.
- SLA: Resins, including specialty formulations for specific applications.
- SLS: Powders (e.g., nylon and composites), offering superior mechanical properties.
Print Quality and Detail:
- FDM: Moderate, suitable for functional but less detailed parts.
- SLA: High, ideal for detailed and aesthetic parts.
- SLS: Moderate to high, depending on the material and application.
Build Volume:
- FDM: Large, with some printers capable of printing over 1 meter in size.
- SLA: Moderate, limited by resin vat size.
- SLS: Large, with the ability to maximize build volume by nesting parts.
Application and Functionality:
- FDM: Prototypes, basic models, and functional parts with straightforward designs.
- SLA: Detailed and aesthetic parts, such as jewelry and dental models.
- SLS: Functional and complex geometries for industrial and mechanical applications.
Detailed Comparison of FDM vs SLA vs SLS
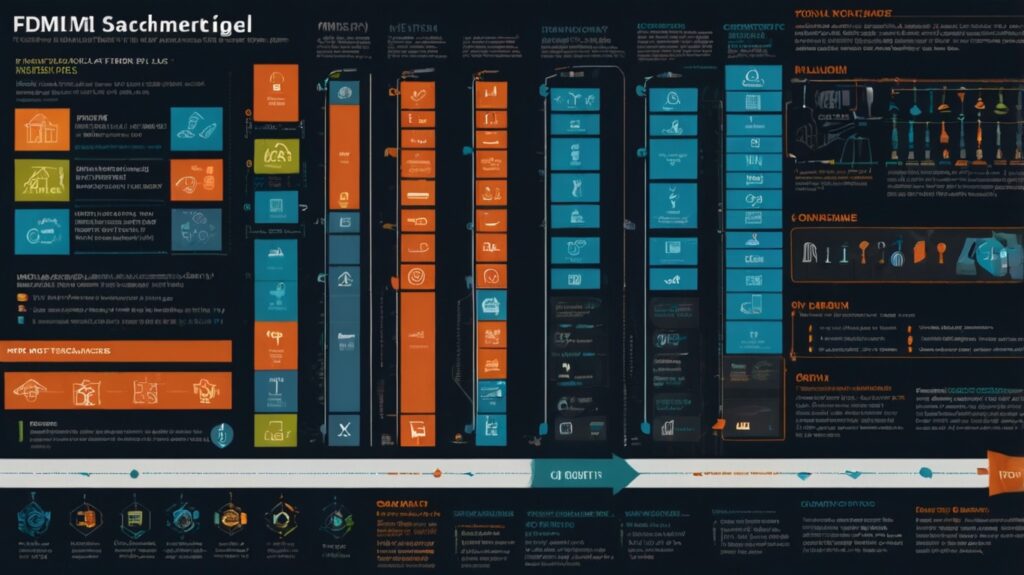
Feature | FDM | SLA | SLS |
---|---|---|---|
Cost | Low | Moderate to high | High |
Precision | Moderate | High | Moderate to high |
Materials | Thermoplastics | Resins | Powders |
Build Volume | Large | Moderate | Large |
Applications | Prototypes, tools | Jewelry, dentistry | Industrial parts |
Advantages and Disadvantages of FDM
Advantages:
- Affordable.
- Easy setup and operation.
- Broad material compatibility.
Disadvantages:
- Limited precision.
- Requires support structures.
- Rough surface finish.
Advantages and Disadvantages of SLA
Advantages:
- Superior detail and finish.
- Suitable for intricate designs.
Disadvantages:
- Expensive.
- Fragile parts.
- Lengthy post-processing.
Advantages and Disadvantages of SLS
Advantages:
- Strong and functional parts.
- No need for support structures.
Disadvantages:
- High cost.
- Complex setup.
When to Choose Each Technique
Ideal Use Cases for FDM:
- Rapid prototyping.
- Budget-friendly projects.
- Functional parts with basic geometry.
Ideal Use Cases for SLA:
- High-detail prototypes.
- Jewelry and artistic models.
- Medical applications.
Ideal Use Cases for SLS:
- Functional industrial parts.
- Complex geometries.
- Durable components.
Conclusion
Choosing the right 3D printing technique depends on your project’s specific needs. FDM is best for affordability and simplicity, SLA excels in detail and aesthetics, and SLS shines in durability and complexity. By evaluating factors like budget, material requirements, and application, you can select the method that aligns with your goals and ensures success.
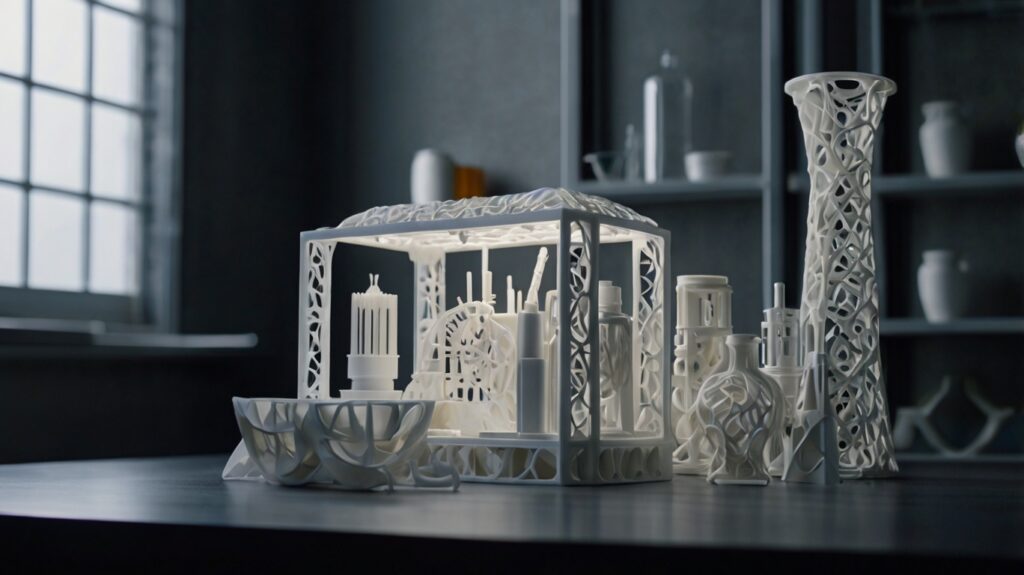
FAQs
Which 3D printing technique is the cheapest?
FDM is the most cost-effective technique, making it ideal for beginners and budget-conscious projects.
Can SLA prints be used for functional parts?
SLA is best for aesthetic and detailed prototypes, but its parts can be brittle and less suitable for heavy-duty functionality.
What materials are compatible with SLS?
SLS commonly uses powdered materials such as nylon, polyamides, and composites for durable and functional parts.
How do I decide between FDM and SLA?
Choose FDM for affordability and simplicity. Opt for SLA if your project requires high precision and a smooth surface finish.
Is SLS suitable for small-scale projects?
While SLS offers excellent durability and complexity, its high cost and setup requirements make it more suitable for industrial applications.