3D printing technologies have evolved significantly over the years, with Fused Deposition Modeling (FDM) and Stereolithography (SLA) being two of the most widely used methods. While both processes allow for the creation of intricate designs, their material properties differ substantially, making them suitable for different applications. This article explores the key differences in material properties between FDM and SLA to help you determine which technology is best for your specific needs.
Table of Contents
Material Types
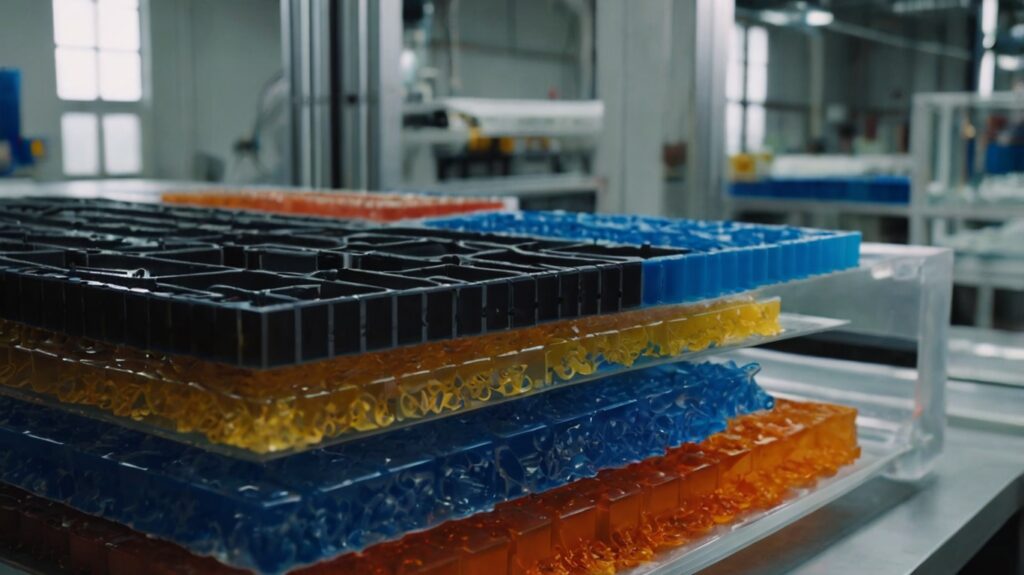
FDM (Fused Deposition Modeling) uses thermoplastic materials, which are solid at room temperature and become pliable when heated. These materials can be extruded layer by layer to form solid parts. The primary materials used in FDM printing include:
- PLA (Polylactic Acid): PLA is one of the most popular FDM filaments due to its ease of use, low cost, and eco-friendly properties. It is made from renewable resources like corn starch or sugarcane and is biodegradable. PLA is ideal for creating models that don’t require high strength or durability, such as decorative items or prototypes. However, it is more brittle than other thermoplastics and may deform under high temperatures.
- ABS (Acrylonitrile Butadiene Styrene): ABS is known for its strength, toughness, and resistance to impact. It is commonly used in industries like automotive and consumer goods for creating functional prototypes, housing parts, and products that need to withstand wear and tear. ABS requires a heated print bed and can release fumes during printing, so proper ventilation is essential.
- PETG (Polyethylene Terephthalate Glycol): PETG is a popular FDM material known for its durability, flexibility, and ease of printing. It has excellent chemical resistance, making it suitable for applications in food containers, medical devices, and industrial components. PETG is stronger and more flexible than PLA, but it is easier to print than ABS, making it a favorite for prototyping.
- Nylon: Nylon is a versatile and durable material widely used for parts that require strength, flexibility, and abrasion resistance. It is often used for creating functional parts, including gears, bearings, and automotive components. Nylon is also known for its low friction properties, making it suitable for parts that need to slide against other surfaces.
- ASA (Acrylonitrile Styrene Acrylate): ASA is a high-performance thermoplastic that is similar to ABS but with improved UV resistance, making it ideal for outdoor applications. ASA is durable, weather-resistant, and capable of withstanding high temperatures, making it suitable for automotive and industrial components exposed to harsh conditions.
SLA (Stereolithography), on the other hand, uses liquid photopolymer resins that cure when exposed to ultraviolet (UV) light. These resins are available in various formulations, allowing for a wide range of material properties. Some common SLA resin types include:
- Standard Resins: These are general-purpose resins used to create prototypes and models with fine details. They are typically rigid, offering good surface finishes but limited in strength. Standard resins are ideal for visual models, concept validation, and display pieces.
- Flexible Resins: These resins offer flexibility similar to rubber and are used for applications where parts need to bend or compress without breaking. They are often used for creating soft-touch components, seals, or medical models requiring flexibility.
- Tough Resins: Designed to mimic the mechanical properties of ABS, tough resins are durable and impact-resistant, making them suitable for creating prototypes or end-use parts that need to handle stress or impact.
- Castable Resins: These resins are formulated for use in the investment casting process. They are used in jewelry making, dental applications, and rapid prototyping where parts are later cast in metal. Castable resins burn out cleanly during the casting process without leaving residue.
- Transparent Resins: These resins allow light to pass through, offering clarity and translucence. Transparent resins are ideal for applications that require light diffusion, such as lens prototypes, or for creating models where visual aesthetics or internal structures are important.
In summary, FDM offers a wider variety of thermoplastic materials, each with distinct properties like strength, flexibility, and impact resistance. In contrast, SLA provides high-resolution prints with resins that offer unique properties, such as flexibility, toughness, or transparency, depending on the application.
Strength and Durability
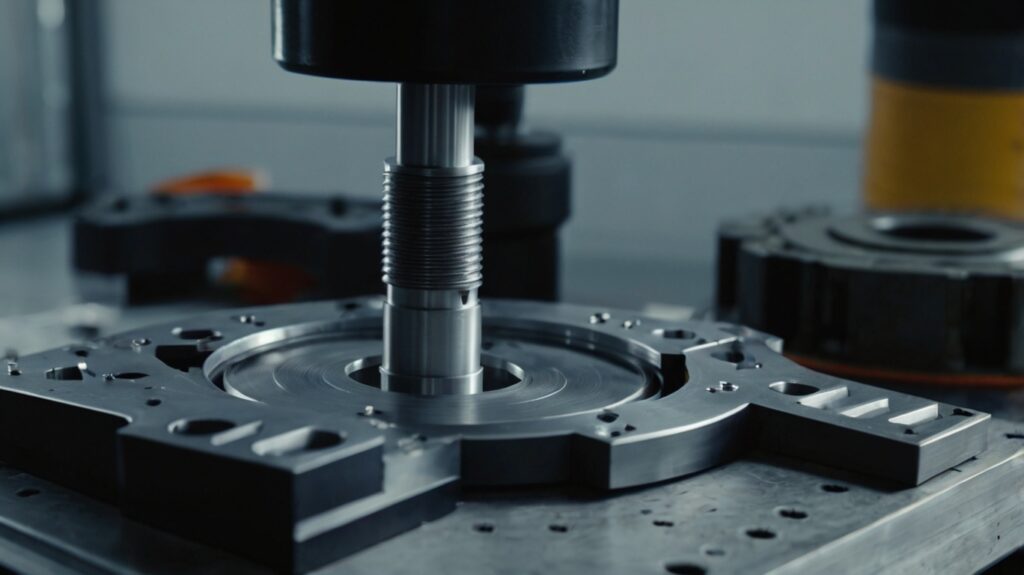
FDM (Fused Deposition Modeling) materials are generally known for their strength and durability, making them suitable for a wide range of functional applications. The strength of FDM prints depends largely on the material used and the print settings, such as layer height, print speed, and infill percentage. Here’s a deeper look at the strength and durability of some common FDM materials:
- PLA (Polylactic Acid): PLA is one of the easiest materials to work with in FDM printing. While it is relatively strong for its weight, it is more brittle compared to other thermoplastics. PLA is suitable for lightweight models and prototypes that don’t need to withstand heavy loads or harsh conditions. However, it is not ideal for parts that will experience high temperatures or stress, as it can deform at temperatures as low as 60°C.
- ABS (Acrylonitrile Butadiene Styrene): ABS is a popular material for functional parts due to its excellent toughness and impact resistance. ABS parts can withstand higher temperatures than PLA, making them more suitable for automotive, industrial, and consumer applications. ABS is commonly used for parts that need to endure mechanical stress, like housings, gears, and structural components. However, it can warp during printing and requires a heated bed to maintain adhesion.
- PETG (Polyethylene Terephthalate Glycol): PETG is a strong, durable, and flexible material that combines the best properties of both PLA and ABS. It has a higher impact resistance than PLA and can maintain its structural integrity in high-stress situations. PETG is ideal for creating parts that need to withstand impact, stress, or exposure to moisture. It also offers better chemical resistance than ABS and can be used for food-safe applications when properly treated.
- Nylon: Nylon is one of the toughest and most durable materials available for FDM 3D printing. It is known for its high tensile strength, abrasion resistance, and flexibility. Nylon is commonly used in industrial applications, such as for creating gears, bearings, and other functional parts that need to withstand wear and tear. It can also absorb moisture, which can affect its print quality, so it is best stored in dry conditions.
- ASA (Acrylonitrile Styrene Acrylate): ASA is similar to ABS in terms of strength but offers improved UV resistance, making it ideal for outdoor applications. ASA parts are resistant to the fading and degradation that often occur when exposed to sunlight, making it suitable for products used in outdoor environments, like automotive parts, signage, and construction components. ASA is highly durable and resistant to both heat and impact.
SLA (Stereolithography) materials, on the other hand, generally have lower strength compared to FDM materials, but they offer other advantages, such as excellent detail resolution and surface finish. SLA resins are often more brittle than the thermoplastics used in FDM, which means that parts made with SLA technology can break more easily under stress. Here’s an overview of the strength and durability of some common SLA resin types:
- Standard Resins: Standard resins used in SLA printing are rigid and can produce highly detailed parts with smooth finishes. However, these resins are generally more brittle than FDM materials and are not suitable for parts that need to withstand heavy mechanical stress or frequent use. They are best for visual prototypes, display models, and non-functional parts that are not subjected to high loads.
- Tough Resins: Tough resins are designed to offer a level of strength and impact resistance similar to ABS. These resins are commonly used in functional prototypes and end-use parts that require more durability than standard resins. While they offer improved toughness, tough resins are still more likely to break under high-impact or high-stress conditions compared to FDM materials like ABS or Nylon.
- Flexible Resins: Flexible resins allow for parts that can bend or compress without breaking. While they offer excellent flexibility, they are not as strong or durable as tougher resins. They are often used in applications such as seals, gaskets, and soft-touch components, where flexibility is more important than structural strength.
- Castable Resins: Castable resins are specifically designed for the investment casting process. These resins burn out cleanly during casting and are often used in jewelry and dental industries. While they do not have the same mechanical properties as tough or flexible resins, they are strong enough for the casting process and provide a smooth finish that makes them ideal for creating complex patterns.
- Transparent Resins: Transparent resins, while ideal for aesthetic applications, tend to be more brittle and are not typically used for functional parts. They are best suited for models that require visual clarity, such as prototypes for optical devices or light diffusion applications.
Comparing Strength and Durability Between FDM and SLA
While FDM materials typically offer greater strength and durability for functional applications, SLA excels in producing highly detailed parts with smooth finishes. If strength is the primary concern, FDM technologies with materials like Nylon or PETG are often the better choice. However, for applications where fine detail, surface finish, and precision are more important than mechanical strength, SLA resins offer significant advantages.
To summarize:
- FDM is ideal for producing functional parts that require strength, flexibility, and resistance to wear and impact.
- SLA is best suited for applications requiring high-resolution details, with tough resins offering some durability but still less than FDM materials.
Surface Finish and Detail
When it comes to surface finish, SLA shines. SLA printers can achieve extremely fine layer resolutions, as small as 25 microns, resulting in parts with smooth surfaces and detailed features. This makes SLA ideal for applications that require high aesthetic quality, such as jewelry or intricate prototypes.
FDM, however, often leaves visible layer lines on printed parts. While this can be mitigated with post-processing techniques like sanding or vapor smoothing, the surface finish of FDM prints will never match the smoothness of SLA prints. FDM is more suited for applications where fine detail is less critical.
Isotropic vs. Anisotropic Properties
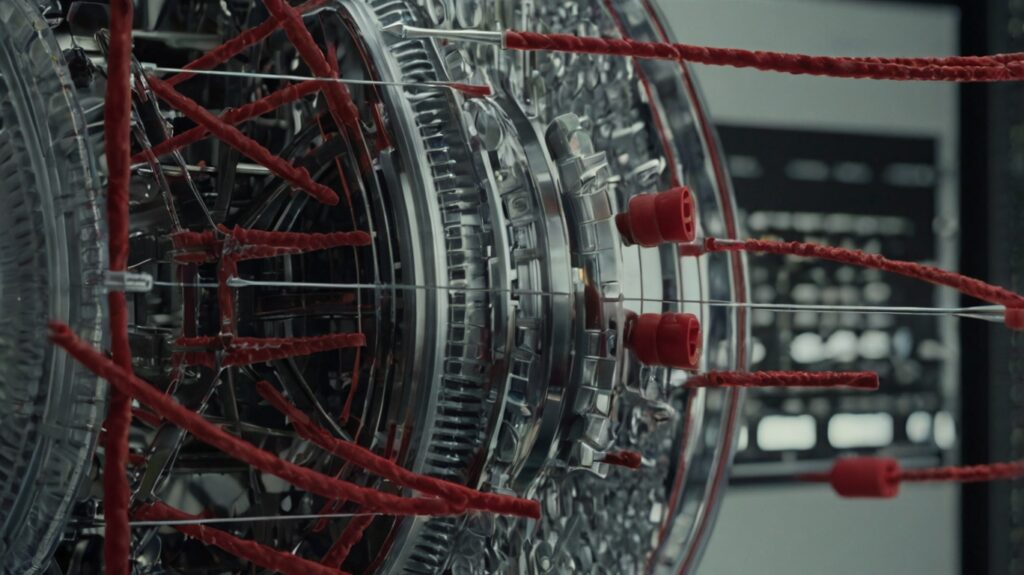
When it comes to FDM (Fused Deposition Modeling) and SLA (Stereolithography), the mechanical properties of the printed parts can differ based on how the material is deposited and cured. This leads to a key distinction between isotropic and anisotropic properties, which influences the strength and performance of the final printed part.
Anisotropic Properties in FDM
Anisotropy refers to the directional dependence of material properties, meaning the mechanical properties of a part differ depending on the direction in which the load is applied. FDM prints tend to exhibit anisotropic behavior, especially because the material is deposited layer by layer.
- Layer Lines: In FDM printing, each layer of material is deposited in a single direction, and the layers bond to each other as the print progresses. This layer-based construction can lead to weaker bonding between layers compared to the bonding within the material of each individual layer. As a result, parts printed using FDM may be weaker along the layer lines when compared to the material’s strength in the horizontal or vertical directions.
- Load Direction: When an FDM part is subjected to mechanical stress, its strength will vary depending on the orientation of the layers. If the layers are aligned in the direction of the applied force, the part may be stronger. However, if the force is applied perpendicular to the layer lines, the part is more likely to fail, as the adhesion between layers is weaker. This phenomenon is especially pronounced in materials like PLA or ABS, which can be prone to layer separation under stress.
- Infill Density and Pattern: The strength of an FDM part can be influenced by the infill pattern and density chosen during printing. Higher infill densities and certain patterns (like grid or honeycomb) can improve the part’s overall strength, but the anisotropic nature of FDM still exists because the bonding between layers is not as robust as the material itself.
Isotropic Properties in SLA
In contrast, SLA produces parts with isotropic properties. Isotropy refers to a material’s uniformity in all directions. In other words, the mechanical properties of a part printed using SLA technology are consistent, regardless of the direction in which the force is applied. This is due to the nature of the printing process and how the resin cures.
- Curing Process: During SLA printing, a photosensitive resin is selectively cured by UV light. The resin solidifies layer by layer, but each layer of cured resin is chemically bonded to the previous one in a way that creates a uniform structure. Since the curing process overlaps the edges of each layer, the result is a much stronger bond between layers compared to the material deposited in FDM. As a result, SLA parts are isotropic, meaning their mechanical properties are largely the same regardless of the orientation of the print.
- Consistency Across Directions: Because SLA parts are isotropic, they tend to exhibit more uniform strength under load, making them less susceptible to directional weaknesses. This can be an advantage in applications where parts need to endure mechanical stress in multiple directions without the risk of breaking along layer lines, such as in precision mechanical components or parts used in demanding environments.
- Material Limitations: However, it’s important to note that while SLA parts exhibit isotropy in their mechanical properties, the materials themselves (e.g., standard resins) are still more brittle and less impact-resistant than the thermoplastics commonly used in FDM printing. For more strength and toughness, SLA users may opt for tougher resins, but even then, the parts will still not match the mechanical properties of Nylon or ABS in FDM prints.
Key Differences Between Isotropic and Anisotropic in FDM and SLA
Property | FDM (Anisotropic) | SLA (Isotropic) |
---|---|---|
Material Strength | Varies based on layer orientation; weaker along layers. | Consistent strength in all directions. |
Layer Bonding | Weaker between layers due to deposition method. | Stronger bonding due to chemical curing process. |
Load Resistance | Strength depends on the load’s direction relative to the layers. | Even strength regardless of the load direction. |
Durability | Can degrade under stress, especially along layer lines. | More consistent durability due to uniform material structure. |
Applications | Best suited for parts where strength in specific directions is needed (e.g., automotive parts). | Ideal for parts requiring uniform strength across all directions (e.g., dental, jewelry). |
Applications
The different material properties of FDM and SLA make them suitable for different types of applications.
- FDM: Due to its strength and versatility, FDM is commonly used in functional prototyping, automotive components, and aerospace parts. Materials like Nylon and PETG are particularly suited for parts that need to undergo mechanical testing or be exposed to harsh conditions.
- SLA: SLA is often used for applications that require high-detail, aesthetic quality, or parts with transparent properties. Industries such as jewelry design, dentistry, and custom prototyping frequently use SLA for its precision and fine detail.
Summary Table: Key Differences Between FDM and SLA Material Properties
Property | FDM | SLA |
---|---|---|
Material Types | Thermoplastic filaments (PLA, ABS, Nylon) | Photosensitive resins (varied properties) |
Strength and Durability | High strength, durable materials (e.g., Nylon) | Lower strength, more brittle parts |
Surface Finish | Visible layer lines, post-processing needed | Smooth, high-resolution finish |
Isotropic vs. Anisotropic | Anisotropic, varying strength based on layer orientation | Isotropic, uniform strength in all directions |
Applications | Functional prototypes, automotive, aerospace | Jewelry, dental models, detailed prototypes |
Conclusion
In conclusion, both FDM and SLA offer distinct advantages depending on the application at hand. FDM is best suited for parts that require strength, durability, and the ability to withstand harsh conditions. Its wide range of thermoplastic materials makes it a versatile choice for functional prototypes and parts that undergo mechanical testing. SLA, on the other hand, excels in creating high-resolution, detailed models with smooth surfaces, making it ideal for applications where aesthetic quality is a top priority.
By understanding the key differences in material properties between FDM and SLA, you can make an informed decision on which technology best fits your project’s needs.
FAQs
What is the main difference between FDM and SLA?
FDM uses thermoplastic filaments that are melted and extruded to create parts, while SLA uses photosensitive resins that cure under UV light. The key differences lie in the materials used, surface finish, strength, and the type of applications suited for each.
Which is stronger, FDM or SLA?
FDM typically produces stronger and more durable parts, especially when using materials like Nylon or ABS. SLA parts, however, tend to be more brittle and are not as resistant to mechanical stress.
Which technology is better for detailed models, FDM or SLA?
SLA is the better choice for detailed models. It can achieve higher resolutions with smoother surfaces, making it ideal for intricate designs and parts that require fine detail, such as jewelry or dental models.
Can FDM be used for functional parts?
Yes, FDM is widely used for functional parts, especially in industries like automotive and aerospace. Materials like Nylon and PETG make FDM a reliable choice for parts that need to endure mechanical stress and environmental conditions.
Is post-processing necessary for FDM prints?
Yes, FDM prints often require post-processing to improve their surface finish, as they tend to have visible layer lines. Methods such as sanding, painting, or vapor smoothing can enhance the appearance of FDM prints.
[…] Discover the Key Differences Between FDM, SLA, and SLS 3D Printing Techniques […]